Although it's not a new technology per se it will have caused the 'offsetmeister' to journey way outside of its usual comfort zone; no doubt entailing some painstaking attention to detail. Cost too, over such a protracted time period, will have been a factor, even in a country that habitually spends 2.5 times as much on its R&D as the UK.
Lengthy and expensive enough surely for wrinkles to have been ironed out, operating performance to have been sharply honed and for one of the industry’s most powerful sales channels to be champing at the bit to reel in ROI before the competition knew what had hit it – not least on short-run late-stage customisation pharmaceuticals packaging applications.
And yet, within three months of rolling out the Linoprint range of DriveLine options at interpack in May (the concept itself having first been unveiled at the previous show three years ago), Heidelberg shells out for one of the very companies whose hard-earned market share you’d have expected it to be decimating instead. Notwithstanding CSAT’s worth and well-deserved reputation, you have to ask yourself why; and why now? The conclusion has to be that CSAT has something that Linoprint is lacking. One obvious possibility is running speed.
Jumping a stage
When Linoprint was first introduced in 2008, 60m/min was confidently talked about; also: "commercialisation in early 2009, with a targeted 10-15 installations completed within the following twelve months". The reality, three years down the road, is
24-28m/min (albeit the average running speed of a thermoformer) and one system integrated within a US-based filling line for a blister-packed OTC product.
Substrate, drop size, resolution and, of course, software can all contribute towards a faster web. In exceeding 40m/min, CSAT appears to have the edge on some of those factors – as they also do with some clever engineering, says late-stage customisation specialist IDI Pac director Chris Waterhouse, who works with both companies on a project basis.
"By pinning an LED lamp between the heads, a skin is created on top of the ink spot, fixing it faster than waiting until the end of the process. Also, they retain excellent tension by running the web over something akin to a little hump-backed bridge. It’s the sort of know-how that’s been helping CSAT to successfully punch above its weight."
"Heidelberg may have found the way to jump a stage," surmises Waterhouse. "Their name and upwards of 40m/min sounds like a winning combination." CSAT’s toner technology also adds a further string to their bow; as does its validation experience within the highly regulated and super-conservative pharmaceuticals market. Indeed, in offering all the main print technologies, this could be a one-stop shop with all the relevant substrates nicely covered.
Des King is a freelance print/packaging journalist
Have your say in the Printweek Poll
Related stories
Latest comments
"Very insightful Stern.
My analysis?
Squeaky bum time!"
"But in April there was an article with the Headline "Landa boosts top team as it scales up to meet market demand", where they said they came out of last year’s Drupa with a burgeoning order..."
"Yep. Tracked is king."
Up next...

Local reports say 100 jobs will go
Landa restructures, seeks investment

Flexible working now integral
BPIF rationalises office space
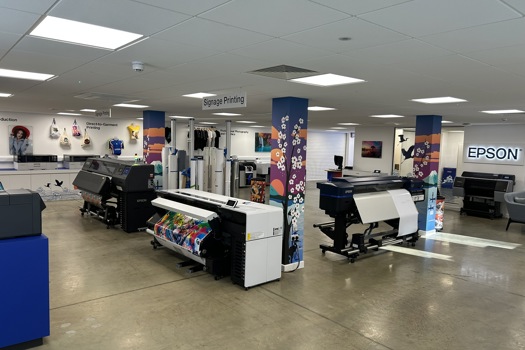
Showcasing commercial benefits
Epson and Fiery to hold ‘Think Big, Print Big’ event

2 July completion target