Unlike the MAN Roland DICOweb, which offers a similar concept, the sleeves will be de-imaged, coated and re-imaged off press.
We decided on an offline system because it delivers several benefits, said international marketing executive James Gann.
The press doesnt stop during imaging, makeready is reduced and capital expenditure is reduced as one Reusable Plate System (RPS) can supply multiple presses.
The Diamond MAX-V has a cut-off range of 546-625mm. Blanket and plate cylinder changes take two minutes, with ink and fount roller train and folder settings automatically adjusted. Its going to change everything forever, said Gann. At Drupa a single unit machine will be shown.
The prototype RPS to be shown at Drupa can produce a new plate in 14 minutes, although the firm expects the commercial version, which will go into test in the Japanese market within two years, to take three minutes.
Story by Barney Cox
Have your say in the Printweek Poll
Related stories
Latest comments
"Gosh! That’s a huge debt - especially HMRC! It’s a shock that HMRC allowed such an amount to be accumulated."
"Whatever happened to the good old fashioned cash job! At least the banks didn't take 2-3% of each sale. After 30 odd transactions that £100 quid you had has gone."
"It's amazing what can be found on the "web" nowadays!"
Up next...

Replacement 'will be operational later this year'
Walstead makes decision on Bicester 64pp
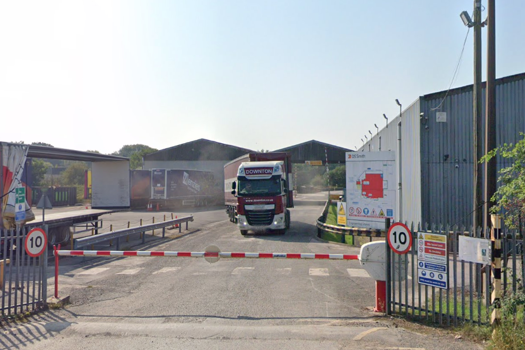
'Ridiculous decision'
Unite “prepared to fight” on proposed DS Smith site closure
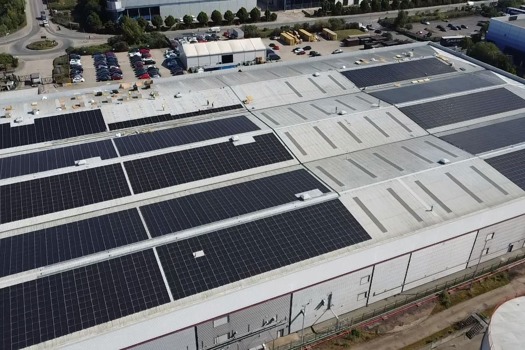
Also helps mitigate volatile energy prices