The 22 employee, £1.6m turnover company specialises in sheet-fed litho and digital print and primarily works with design companies.
Managing director Ian Dodds said the company was installing the MIS over the course of November as part of a drive to reduce administration costs per job.
"We send out between 50 and 80 estimates a day. But, with the arrival of digital printing, the average cost per job has fallen so we needed to adjust to that," he said.
For the last twenty years Billingham Press has used three separate systems to manage production, pricing and accounts. Dodds said the new MIS gives the company more time to pursue market objectives rather than getting caught up in "the minutiae of admin".
The MIS has an estimating wizard with a drag-and-drop function. This allows staff to choose the specifications that are relevant to the customer’s order from a list then drop them into a tray.
The system then calculates the customer’s requirements automatically and creates an estimate. This is then sent to the customer as well as Billingham Press’ factory and studio.
As well as saving the company time on administration, Dodds said the MIS makes it easier to manage jobs by allowing staff to trace the stage they are at and the department that is dealing with them.
Tweet
Have your say in the Printweek Poll
Related stories
Latest comments
"Very insightful Stern.
My analysis?
Squeaky bum time!"
"But in April there was an article with the Headline "Landa boosts top team as it scales up to meet market demand", where they said they came out of last year’s Drupa with a burgeoning order..."
"Yep. Tracked is king."
Up next...

Local reports say 100 jobs will go
Landa restructures, seeks investment

Flexible working now integral
BPIF rationalises office space
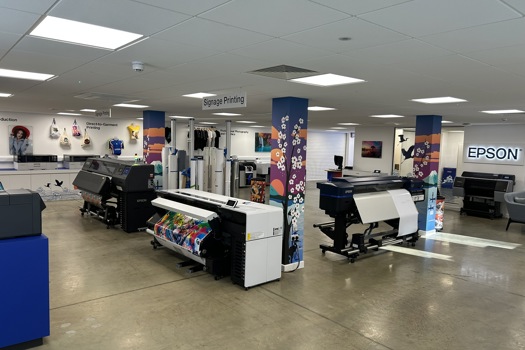
Showcasing commercial benefits
Epson and Fiery to hold ‘Think Big, Print Big’ event

2 July completion target